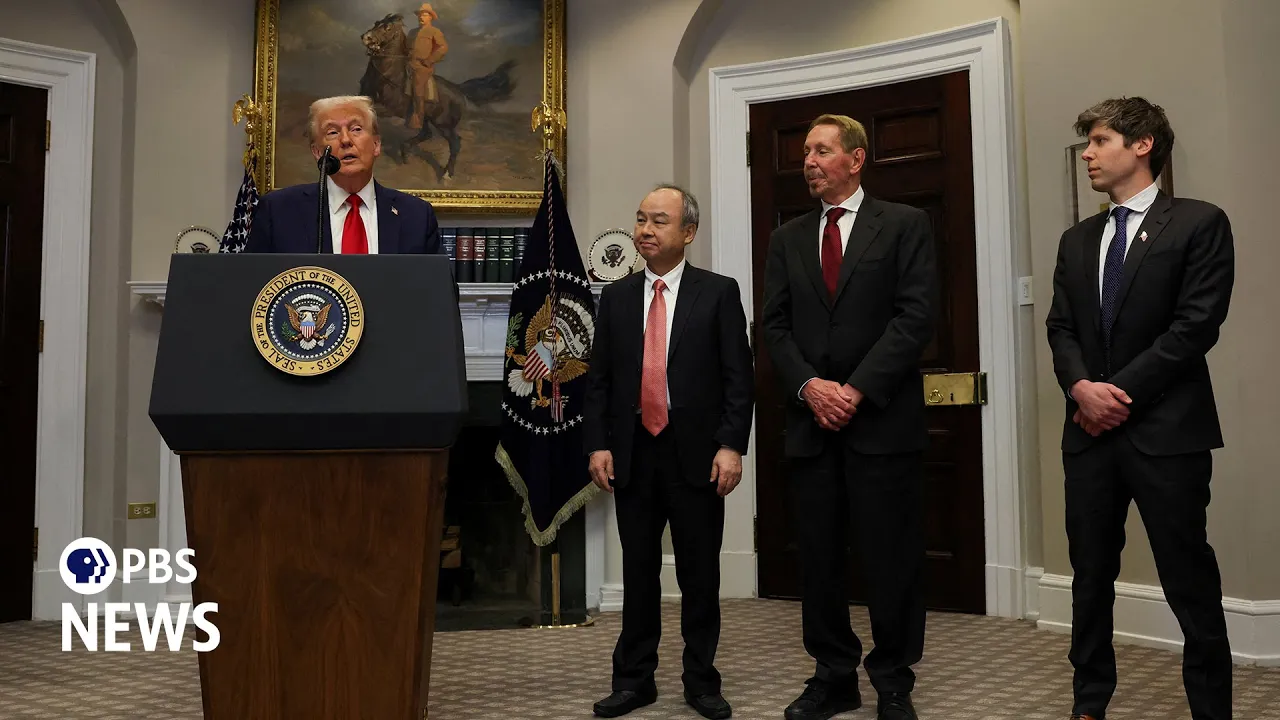
Industrial Insights
July 10, 2025
2025 Supply Chain Manufacturing Outlook: Addressing Deficits and Disruption Across Industries
Navigating Uncertainty and Deficits in a Complex Operating Environment Across Industries
Manufacturing and supply chain leaders face persistent deficits and mounting challenges in 2025. Geopolitical tensions, extreme weather events, and labor shortages create a complex risk landscape that demands strategic adaptation and operational resilience.
Current Market Conditions
The global manufacturing sector enters 2025 confronting a multi-dimensional crisis characterized by supply chain vulnerabilities, capacity constraints, and evolving trade dynamics. While some pandemic-era disruptions have stabilized, new challenges have emerged that threaten operational continuity across critical industries. Labor shortages have become the predominant concern for manufacturers, affecting 77% of companies and surpassing even tariff uncertainty as the primary operational challenge.
Key Manufacturing Metrics:
U.S. capacity utilization declined from 80% (early 2023) to 74.1% (Q1 2025);
Performance remains below the long-term historical average of 79.98%;
Cost pressures from raw materials, energy, and labor continue compressing margins.
This downward trend reflects broader economic uncertainty and demand volatility affecting industrial production.
Cost pressures from raw materials, energy, and labor continue to compress margins, prompting manufacturers to restructure operations through facility closures, workforce reductions, and production schedule adjustments.
Manufacturing Capacity and Production Trends
U.S. industrial capacity utilization has experienced a notable decline over the past two years, with manufacturing facilities operating significantly below optimal levels. The manufacturing sector's capacity utilization rate stands at 74.1% in the first quarter of 2025, representing a modest 0.3 percentage point increase from the previous year. However, this improvement masks underlying structural challenges that continue to constrain production efficiency.
Economic and Financial Pressures
Manufacturing companies are grappling with persistent cost inflation across multiple dimensions. Raw material costs, energy prices, and wage inflation continue to rise, with many manufacturers unable to fully offset these increases through pricing adjustments. The combination of higher input costs and constrained capacity utilization is compressing margins and forcing operational restructuring across the sector.
Companies are implementing cost reduction strategies including facility closures, workforce reductions, and production schedule modifications. Microchip Technology, for example, closed its Tempe, Arizona fabrication facility and reduced headcount to achieve approximately $90 million in annual savings. Similarly, FuelCell Energy implemented a 22% workforce reduction across the U.S., Canada, and Germany as part of a global restructuring plan.
Critical Industry Vulnerabilities
Different industrial sectors face varying degrees of supply chain vulnerability, with technology-intensive industries experiencing the most severe disruptions. Semiconductors, medical supplies, and electronics represent the most critically impacted sectors, while traditional industries such as textiles and energy show relatively lower disruption levels.
Automotive Manufacturing

The automotive sector continues to face significant supply chain challenges that extend beyond semiconductor shortages. Rivian Automotive reduced its 2024 production guidance by up to 10,000 vehicles due to ongoing parts shortages, while Porsche experienced aluminum supply disruptions following flooding at a supplier facility.
These incidents highlight the sector's vulnerability to both component shortages and extreme weather events.
Automotive manufacturers are implementing strategic inventory management and production prioritization strategies. According to a 2023 annual and sustainability report from Porche, the automaker's approach includes detailed component analysis to determine optimal inventory levels and prioritizing specific vehicle models during shortage periods to maintain production flo.
Food and Agriculture

The food sector faces dual challenges from biological threats and climate impacts. Bird flu outbreaks resulted in the loss of nearly 40 million commercial table egg layers across 12 states in 2024, creating persistent supply shortages and elevated prices that are expected to continue through 2025.
The U.S. Department of Agriculture's data indicates these disruptions will have lasting effects on food production where eggs are primary ingredients.
Cocoa supply chains face additional pressures from weather-related disruptions and labor issues in West Africa, which produces over 70% of global supply.
These challenges have forced candy manufacturers like Hershey to increase production of non-chocolate products to maintain market presence amid rising input costs.
Medical Supplies and Pharmaceuticals

Medical supply chains demonstrate particular vulnerability to natural disasters and concentrated production. Hurricane Helene's impact on IV fluid production facilities created nationwide shortages that persist into 2025, with empty IV bags of all sizes in critical shortage.
Baxter's North Carolina facility damage illustrates the risk of geographic concentration in critical medical supply production.
The FDA has identified systemic weaknesses in medical device shortage reporting, warning that the U.S. lacks mandatory reporting requirements that could enable proactive shortage prevention.
This regulatory gap represents a strategic vulnerability in healthcare supply chain resilience.
Semiconductor Industry

Despite ongoing supply challenges, the semiconductor sector shows signs of stabilization with improving inventory levels. Taiwan Semiconductor Manufacturing Company reports expectations for healthier inventory levels in 2025 compared to 2024, though AI-related demand continues to outpace supply in certain segments.
The CHIPS and Science Act is providing substantial investment support, with companies like Microchip Technology receiving $162 million in funding to expand domestic production capacity. However, implementation timelines remain extended, with facility construction requiring approximately two years from groundbreaking to initial production, not including pre-permitting phases.
Key Risk Factors
Risk Factor | Impacted Sectors | Description |
Geopolitical Tensions | Automotive, Energy, Tech | Tariffs and trade barriers disrupt cross-border supply and increase costs. |
Extreme Weather Events | Automotive, Food, Medical | Floods, hurricanes, and droughts damage facilities and disrupt agricultural and industrial output. |
Labor Shortages | All Sectors | Difficulty sourcing skilled workers delays production and facility ramp-up. |
Regulatory Uncertainty | Medical, Tech | Gaps in reporting and oversight hinder proactive shortage management. |
Geopolitical and Trade Policy Uncertainty
Trump's tariff expansion targeting Canada, Mexico, and China represents a significant escalation in trade policy that will fundamentally reshape North American industrial supply chains. These measures threaten to create critical material deficits across energy, manufacturing, and automotive sectors while forcing companies into costly supply chain restructuring.
Tariff implementation poses a significant operational risk for North American supply chains, with proposed duties on Canadian and Mexican goods threatening critical sectors including energy products, pulp and paper, and automotive parts. Canadian imports are particularly vulnerable given the integrated nature of cross-border trade relationships, where tariffs could trigger supply shortages across these key industrial segments and force manufacturers to seek alternative sourcing arrangements at potentially higher costs.
President Donald Trump said he plans to implement a 10% tariff on China-based imports during a press briefing at the White House on Jan. 21, 2025.
Complex trade relationships create a challenging paradox for manufacturers: while companies actively pursue supply chain rerouting and supplier diversification to avoid tariff impacts, these very mitigation efforts can trigger temporary operational disruptions during the transition period.
The adaptation process involves multiple interconnected challenges. Companies must identify and qualify new suppliers globally, restructure logistics networks to accommodate different shipping routes, and navigate increasingly complex cross-border administrative requirements. Shippers face the dual burden of evaluating alternative suppliers worldwide while simultaneously managing price increases from existing partners affected by tariff policies.
This transition period is particularly vulnerable to supply shortages, especially when tariff-driven cost increases make certain sourcing options economically unviable. The result is a cascading effect where companies abandon cost-prohibitive suppliers faster than they can fully qualify replacements, creating manufacturing delays that ripple through production schedules and delivery commitments.
Current tariff policies have already impacted operations, with some manufacturers experiencing temporary disruptions. For example, tariffs imposed on the United States-Mexico-Canada Agreement (USMCA)-compliant goods from Mexico during March 4-6, 2025, created unexpected cost burdens that companies were unable to pass through to customers due to the brief implementation period.
Labor Market Constraints
Skilled labor shortages have become the most critical operational constraint facing manufacturers, affecting production capacity, innovation capabilities, and operational flexibility. The manufacturing sector faces particular challenges in attracting younger workers, with traditional career paths less appealing to emerging generations.
Companies are responding through workforce development initiatives, including apprenticeship programs, partnerships with educational institutions, and enhanced compensation packages. However, these solutions require significant lead times and investment before generating meaningful impact on production capacity.
Climate and Weather Risks
Extreme weather events continue to create supply chain vulnerabilities, particularly for industries with concentrated production facilities. Hurricane Helene's impact on medical supply production and flooding at automotive supplier facilities demonstrate the ongoing risk of climate-related disruptions.
Manufacturing facilities in regions prone to natural disasters face particular exposure, requiring investment in resilience measures and geographic diversification strategies to maintain operational continuity.
Supply Chain Resilience Enhancement
Manufacturers should prioritize supplier diversification and geographic distribution of critical components. The concentration risk highlighted by Richie Daigle of Tive remains a fundamental vulnerability that requires systematic mitigation through multi-sourcing strategies.
Companies should implement advanced analytics and AI for supply chain monitoring and predictive risk management. These technologies enable real-time visibility and proactive response to emerging disruptions.
Operational Optimization
Manufacturing flexibility and agile production capabilities are essential for managing demand volatility and supply constraints. Companies should invest in scalable production systems and cross-trained workforce capabilities to adapt rapidly to changing conditions.
Implementing lean manufacturing principles and continuous improvement processes can help optimize resource utilization while building operational resilience.
Workforce Development
Strategic workforce planning must address both immediate staffing needs and long-term skill requirements. Companies should establish partnerships with educational institutions and invest in internal training programs to build sustainable talent pipelines.
Automation and technology integration can help address labor shortages while enhancing productivity and consistency. However, this requires careful workforce transition planning to maintain operational continuity.
Financial and Risk Management
Companies should implement comprehensive risk assessment processes that evaluate operational, financial, and strategic exposures across the supply chain. This includes stress testing scenarios for various disruption types and developing contingency plans.
Working capital optimization and flexible financing arrangements can provide operational buffer during disruption periods while maintaining investment capacity for resilience enhancement.
Strategic Recommendations
Diversify suppliers and production locations to mitigate concentration risks.
Adopt advanced analytics and AI for real-time supply chain monitoring and predictive risk management.
Invest in workforce development through training, apprenticeships, and automation to address labor shortages.
Enhance operational agility by implementing lean manufacturing and flexible production systems.
Develop robust contingency plans for geopolitical and climate-related disruptions.
Manufacturing Market Outlook
The manufacturing sector outlook for 2025 remains cautiously optimistic despite persistent challenges. While capacity utilization trends show gradual improvement in some sectors, the operating environment will likely remain volatile through the year.
Technology adoption and automation investments are expected to accelerate as companies seek to address labor constraints and enhance operational efficiency. The integration of AI, IoT, and advanced analytics will become increasingly critical for competitive positioning.
Reshoring and nearshoring initiatives will continue gaining momentum as companies prioritize supply chain security over cost optimization.
The convergence of geopolitical tensions, climate risks, and technological transformation creates a complex operating environment that demands adaptive strategies and continuous risk management. Companies that successfully navigate these challenges through strategic planning, operational excellence, and stakeholder collaboration will be positioned for sustainable growth despite ongoing uncertainties.
Related articles
Our platform is designed to empower businesses of all sizes to work smarter and achieve their goals with confidence.